|
Moving forward on KY’s custom baby wrap, I got bout 4 wound. Not 4 colors like I’d said in my last post, but 3: chambray, bleu cobalt and bleu moyen.
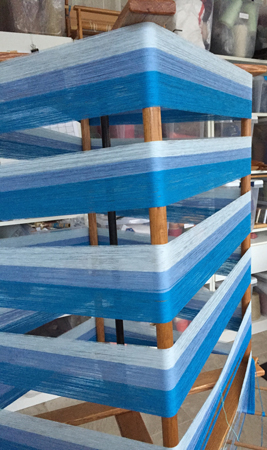
Next step is to get it on the loom. I always do this under tension, using my version of a warping valet. (Unending thanks to Laura Fry for this…makes my life so much easier.)
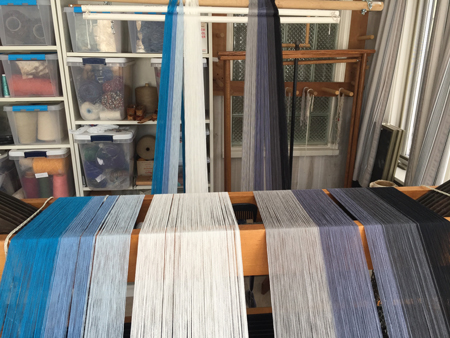
As always, one of my favorite shots is the warp as it’s being wound on the back beam.
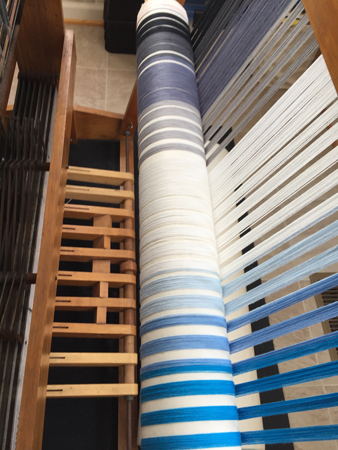
Then I threaded 758 threads through the heddles and the reed, securing them with a slip knot as I work across the width of the piece.
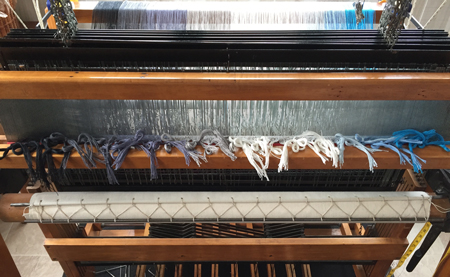
After that I have to check for tension issues, and to make sure I don’t have any threads crossed in the reed. The slats from an old Venetian blind work for this purpose and make a nice, hard surface for the weft. It all looks good.
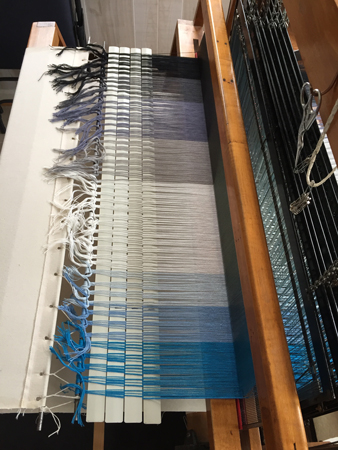
So I wind bobbins and start weaving. Somehow I manage to get several motifs woven before I notice the problem.
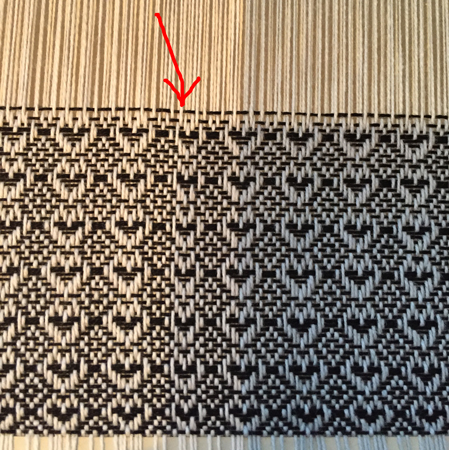
I have missed threads, shaft 4 on both the way up and the way down the threading V. Nothing to do but take out what I’ve done and fix the error. I decided to cut the weft threads in roughly the middle and remove them in pieces. Here I’ve removed the threads on the right side of the loom.
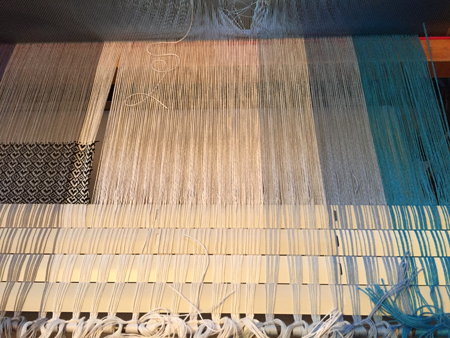
And here’s what the process looks like mid-stream on the left side.
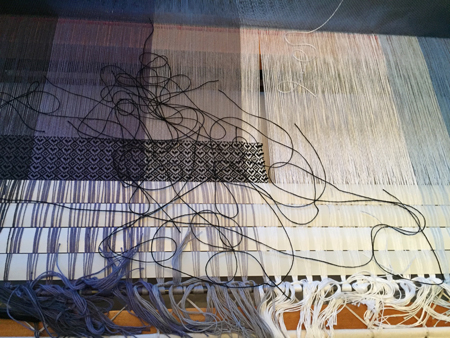
Then I made 2 string heddles for shaft 4, hung new threads for those 2 spots. Next I had to remove the threads from the reed from the error all the way to the selvedge, re-threading the reed. If I didn’t do that I would have had a spot where the threads were too close together and it wouldn’t have felt or looked right.
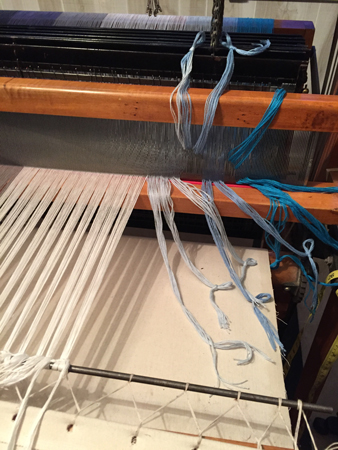
Finally I got the threads all tied onto the apron rod again. And now I needed to walk away for a while, giving both my brain and my body a rest.
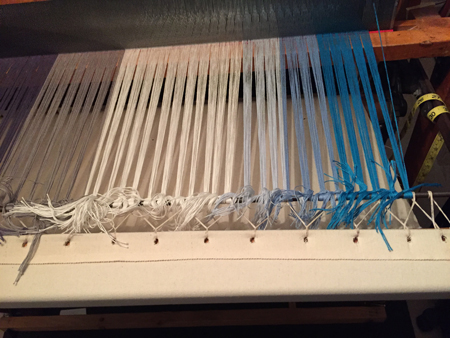
This morning I spread the warp with scrap threads, treadling in order, instead of using those spacers from the blind, as they couldn’t tell me if there were other threading errors. It looked okay, although it was hard to see with the pale and changing colors. So I again started weaving with KY’s black tencel.
Poop!!! Another error!! This time in tie up. A hook had popped off one of my treadles. Can you see the difference? Look closely at the first and second rows of black hearts. The first row has the error. Thankfully I spotted it quickly and fixed it easily.
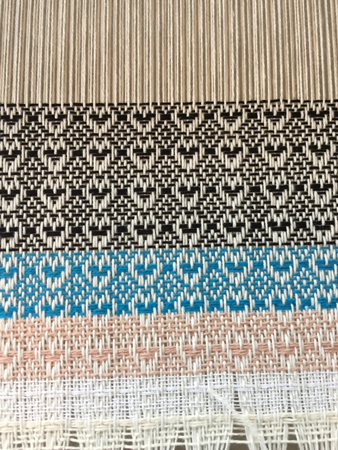
I’m finally on my way! I got about 45″ woven today.
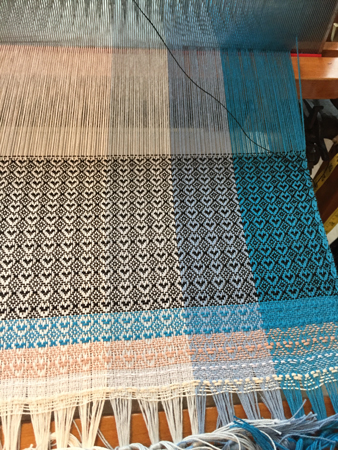
Not much, considering it’s taken me many days to get to this point. And after I weave off the 15 yards of this warp and do all the inspecting and other off-loom work, I have 2 other custom weaving jobs waiting, one for a shawl, the other for a scarf. The Weaving Center has been taking up lots of my time. I think that should slow down dramatically soon, but probably not till February 1.
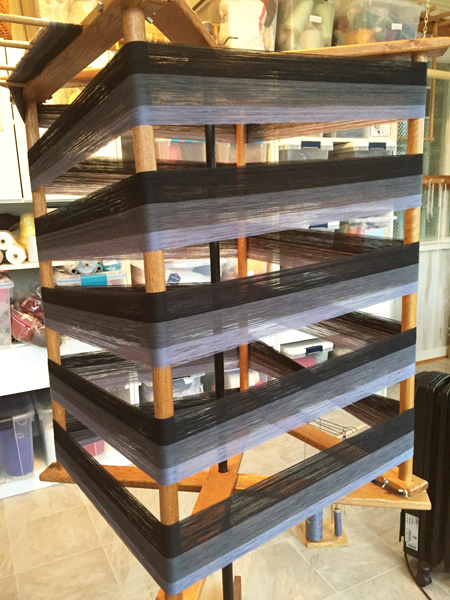
I just finished the last of my Christmas gifts this morning. Whew! I’ll be sharing them on Sunday, so can do a post with my gift handiwork next week.
So yesterday afternoon I took a break and wound bout 1 of KY’s custom baby wrap. Honestly, my body was not used to how many times I have to go around for these really long warps. This one is 15 yards long. From top to bottom the colors are black, charcoal and dark gray. Mom chose for me to use a combination of my usual Maurice Brassard cottons and Egyptian cotton.
Today I wound bouts 2 and 3.
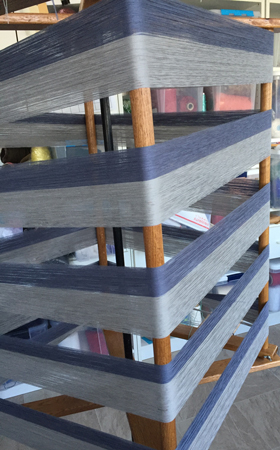
Bout 2 finishes the dark gray then goes to light gray. Interesting how proximity and the lighting makes the bottom of bout 1 look completely different than the top of bout 2, isn’t it? But they are identical it’s the same yarn.
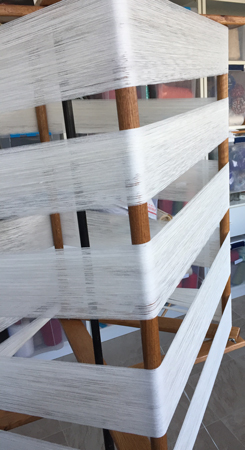
Bout 3 is solid white. My back is done with this activity for the day, but I’m looking forward to bout 4, which as 4 colors of blue in it.
I’ve also been going round and round elsewhere in my life. You know that saying that no good deed goes unpunished? Here I am. 😉
Back in November I wrote a small grant application for a project for the Weaving & Fiber Arts Center. I just learned on Monday that we were funding for my full request (which was just over $1,000). So now it’s implementation time. As the (volunteer) General Coordinator of this (volunteer-run) organization, guess who gets to do that? 🙂
The project is to deliver hands-on fiber arts activities to high school and college students in 3 different programs. The first program is scheduled for November, during a school break, so I had to immediately spend a bunch of time online gathering email addresses for high school and college art teachers, then send them individualized emails. But before I could do that I had to learn the Weaving Center’s online registration software so I could write a clear description and put it up online. Essential for me to be able to share this info with the teachers.
Since the class is limited to a maximum of 12 students, I opted to email only the high schools that are geographically closest, or that we already have a (limited) relationship with. Still, that was 28 emails. Even with copy & paste, it’s all time consuming.
And now I’ve committed to writing another small grant, for a one-shot project to coordinate a weaving program scheduled for July with the local Bhutanese community. Ay yi yi.
Following a pattern established by Meg over at Unraveling, even though she’s apparently not playing the game this year, I took shots of my looms as they stood on New Year’s Day, 2017. In no particular order….
This is a shot of the treadles of my Macomber. I like this angle, even the fact that you can see some lint in the slot of the treadles. There’s no warp on this loom at the moment, although I have three orders that will be woven on it over the next few weeks.
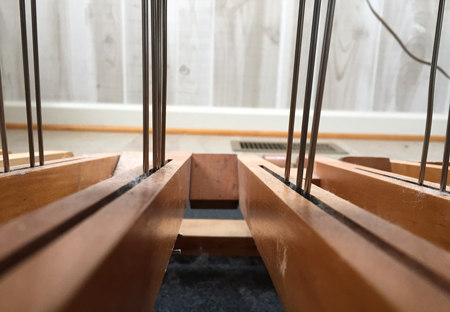
Next is my rigid heddle loom. This little loom is currently both happy and sad. All that lint in the heddle is a reminder that it had a project on it not that long ago…it wove a lovely alpaca houndstooth scarf that sold very quickly in my Etsy store. You can also see the ends of some wood sticking out underneath it. I bought the pieces needed to add a second heddle to the loom, which will make it even more versatile than it already is. It’s happy about those two things, even though it spends most of its life on a top shelf in the weaving studio.
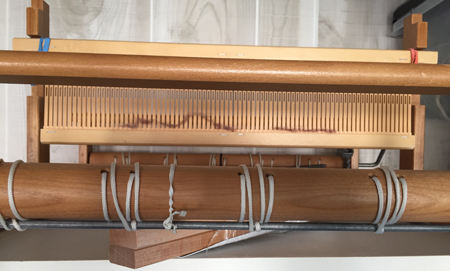
My sweet little counterbalance loom is currently acting as a catch-all. 🙁 A towel, bobbins, a book, yarn, samples, all just resting on her. A warp is not currently in the planning for her, either.
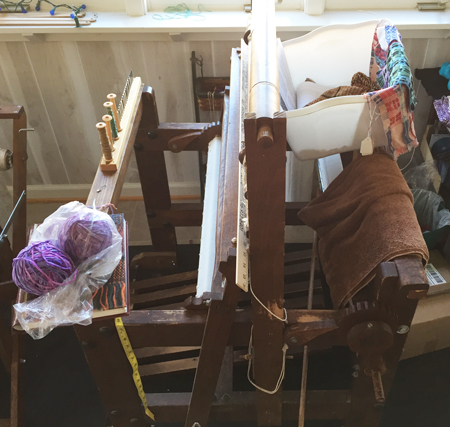
Even sadder is the Missouri, stored in the attic. It did make it down for the supplemental warp workshop, but spends 98% of its time alone in the dark and either freezing or roasting under the eaves.
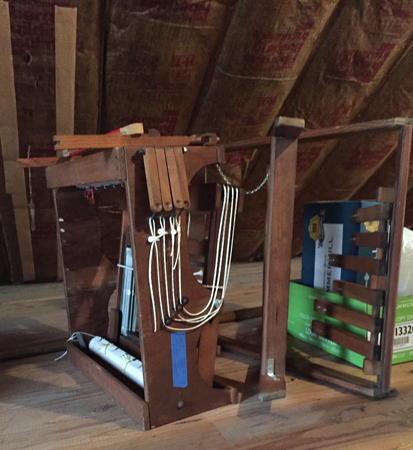
So why oh why is there a newcomer? Who the heck is this and why is it here?
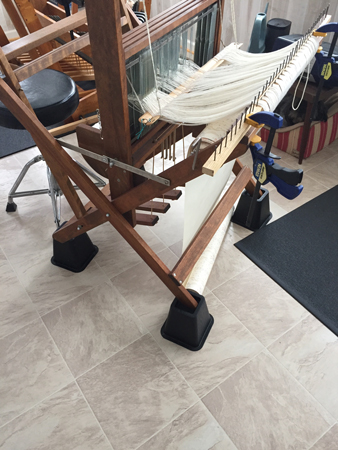
Well, at the supplemental warp workshop I got a chance to weave on someone else’s Dorset loom. I really liked it. It’s a 4 shaft, direct tie up, folds for transport, well made, decent length from front-to-back beam makes for a decent shed. Well respected little loom, made by FC Wood in Waterford, NY. Hasn’t been made in decades. Not a ton of them around. Several other loom manufacturers have copied the design either directly or some with modifications. I decided I wanted to see if I could find a Dorset loom to buy, and if I could, I’d sell both the counterbalance and the Missouri.
I was lucky enough to find one within the Rochester Weaver’s Guild! I snapped it up, and have put a towel warp on it to make sure I like weaving on it before I sell the other two looms. Actually the above photo was taken a few days ago, when I was threading the loom. It’s not the most comfortable loom to thread, so I put it up on bed risers to make it a little easier. That made me cautious and hesitant about my purchase. But once I had it set up, wow. Weaving is a dream. And this spoken by someone who’s never had a direct tie up loom before and didn’t like working on one.
For you non-weavers, direct tie up means that there are only 4 treadles, one for each shaft, and each treadle can only be tied to one shaft. So when you’re weaving, you most often need to use two feet at the same time. Just to weave plain weave you’re lifting 2 shafts at once. I wasn’t sure I’d really like it, but I do. It is remarkably easy to treadle, and since there is no changing of the tie up, there’s one less step to set up for each pattern. I can change the weave pattern mid-stream if the spirit moves me. On my other floor looms changing the weave pattern often necessitates crawling under the loom and changing how the treadles are tied to the shafts.
So yes, I will be posting my counterbalance and Missouri looms for sale. They’ll both be very affordable, and I’m hoping that a relatively new weaver will jump on them. That would make me really happy. Especially for the counterbalance. She’s been a sweet loom and deserves continued attention and use. Know anyone who might be interested?
He needs your help. I don’t know how to help him.
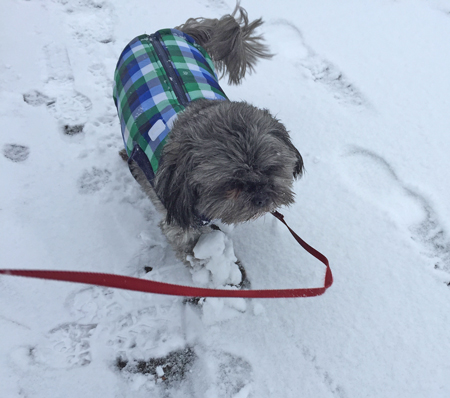
He’s the third dog that I’ve owned that with this issue and I haven’t known how to help any of them. I’ve tried a few strategies, none successful, so I’m turning to you. Have you had an animal with similar problems? If so, have you figured out how to either prevent or solve it?
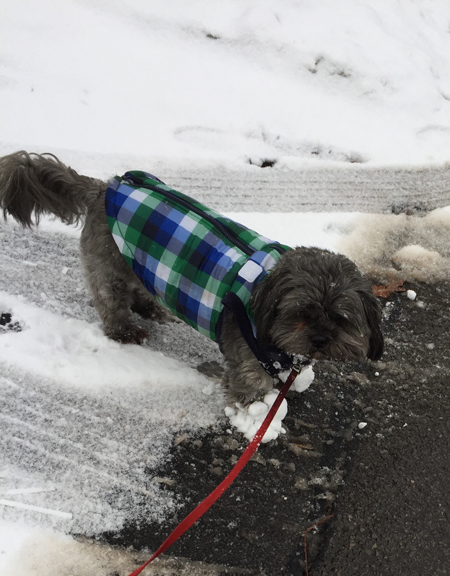
Have you seen the problem in the first two photos? If not, the third is totally clear. When the snow is wet and heavy, the kind of snow that would make good snowballs or snowmen, Jack’s feet make snowballs as he walks, eventually growing big enough to pull on his hair.
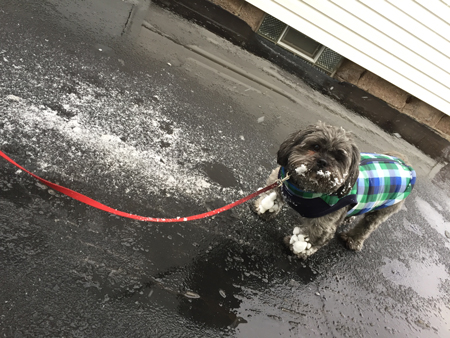
These snowballs gather and get bigger as he walks. I find it curious that the snowballs aren’t gathering on his back feet; on my previous dogs the problem was with all 4 feet.
I’ve tried boots, which he definitely dislikes. Plus since his legs are so thick, it’s almost impossible to get them tight enough that he doesn’t lose them. On previous dogs I’ve tried lifting them into the sink or tub and using warm water to quickly melt off the snow. None of us liked that. I’ve tried keeping the hair on the legs really short. Not a good plan in the winter either, especially with someone like Jack who gets cold rather easily.
So readers, what are your suggestions to help this little guy?
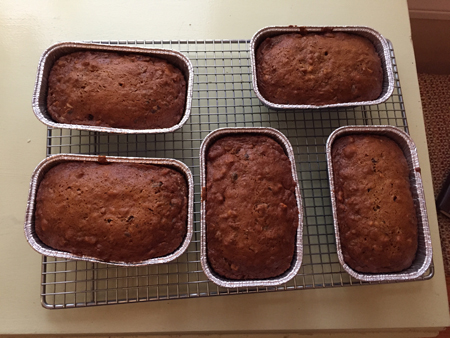
It’s Christmas Eve. I’ve baked my grandma Troiano’s date nut bread and grandma Cherre’s pizzelles, chocolate-peanut-butter balls (some call them buckeyes), my sister’s most excellent recipe for ginger cookies that include lots of freshly grated orange peel, and some cinnamon biscotti. The first three are major traditions in my family.
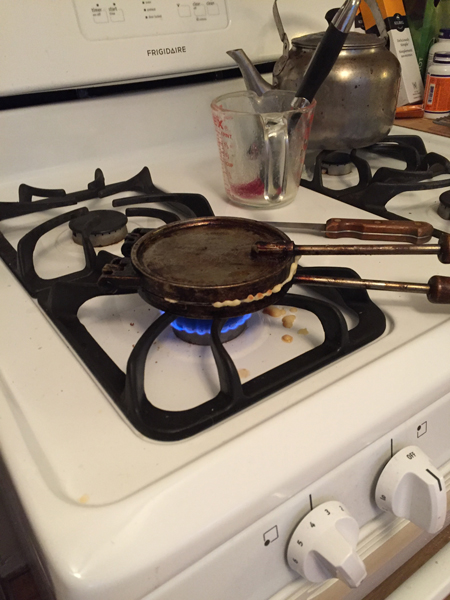
I’m still knitting a present, and can’t yet show you any of the finished things, but I can show you my wonderful hat.
Sometime this summer I took a felting class at the Weaving and Fiber Arts Center. Trust me when I tell you that I’d never felted before, and that I still don’t really understand the process – it seems like magic to me.
I started with dyed wool roving. Or maybe it’s correctly called top. In any case, here’s how it looks.
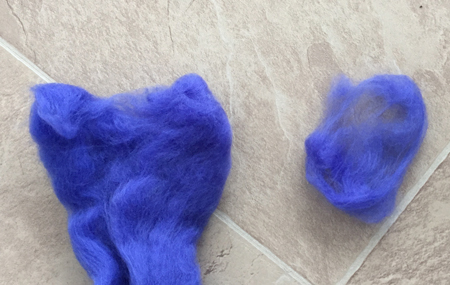
It’s not yarn, it’s not fabric, it’s fiber. You pull it out in really thin strands, lay it on top of a plastic template called a release, wave your hands over it, turn around three times, say the magic words, and it ultimately turns into a solid fabric. For this class that fabric was shaped over a hat form, where it dried. Can you see the fine little silk threads a felting neighbor gave me to put in with the wool for a bit of interest?
I took the hat home and had to add an embellishment and do a blanket stitch along the edge for stabilization. I didn’t want to do the edge stitching until I’d decided on the embellishment because I wanted them to coordinate. It took me months to figure out what I wanted that embellishment to be.
Finally I did – a crocheted ‘flower’ of sorts, with a beaded center. If something else strikes me in the future I can easily take this off and replace it. For that reason I decided I wanted the blanket stitching to be almost invisible.
I am very happy with my wool hat!
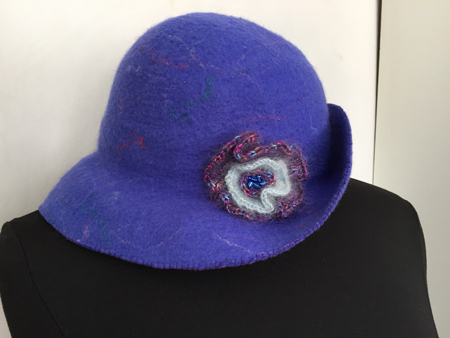
|
|