While I was weaving those lovely blue striped & plaid towels I had an idea for one more warp of towels I wanted to try – somewhat fancier towels, in a somewhat smaller size, white with a colored overshot border. More tea towels than dish towels.
For non-weavers, overshot is a traditional type of weaving, with a thicker colored weft making patterns and a thinner, often white, weft holding those pattern threads in place. Coverlets were typically woven in overshot. I’d seen some absolutely stunning weaving with overshot borders and wanted to do some, even though weaving with multiple shuttles isn’t my favorite thing to do.
I decided on a pattern, measured out 362 threads about 9 yards long, set up the loom, and was off. My warp & tabby weft were an 8/2 unmercerized cotton and I used a doubled 5/2 mercerized for the pattern weft. I wove the first end twice, and trust me when I tell you that unweaving overshot is NOT fun. So why did I do it twice? Because it appeared I’d made a weaving error. However it turned out I didn’t. I went very slowly the second time and it was exactly the same. It was apparently all about how the tabby fit – when it was a 1-3 tabby and when it was a 2-4. So I wove the rest of the towel and then did the pattern at the other end. Same thing. I cut them off the loom and wet finished them to see if the look changed. It didn’t. Here’s the finished towel showing both ends.
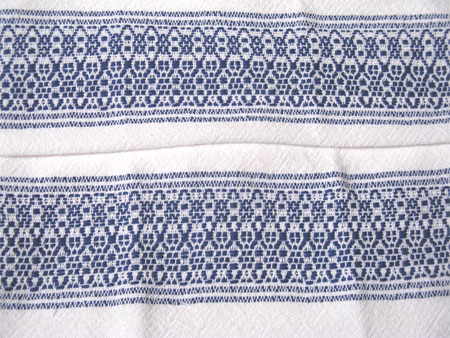
Being as hung up on symmetry as I am, these towels just didn’t keep me happy. I also didn’t think that the doubled 5/2 weft was still thick enough to work — too much white in the pattern.
So it was back to the computer to redesign. What else could I do with the threading I’d chosen that would make me happy? I decided I’d stick with the doubled 5/2 for the pattern weft but do a regular twill weave so that the pattern would stand out more. The threading lent itself to many treadlings.
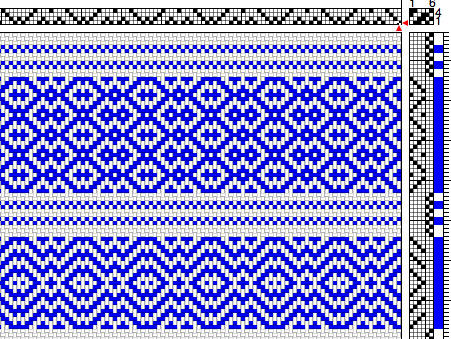
First I wove three towels with a navy weft. I like all 3 patterns, but figured not everyone wanted blue.
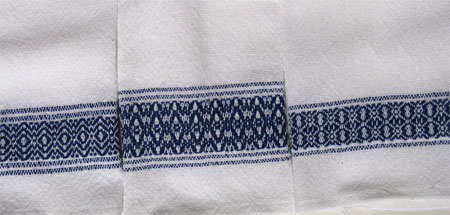
So next I did two more treadlings with a cranberry weft.
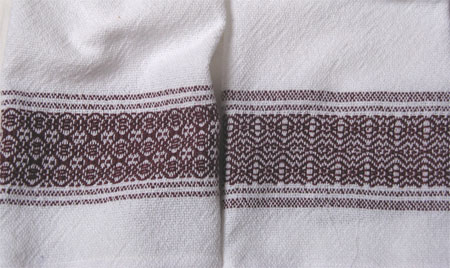
Then I went with a lilac thick-thin cotton for two towels.
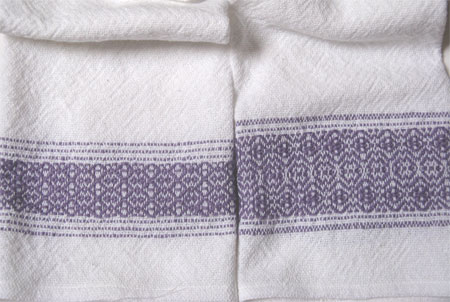
I finished out the warp with an interesting weft that’s a blend of cotton & linen.
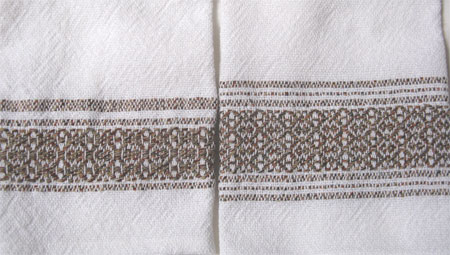
I find it interesting that the plain weave sections of these towels appear to have some type of pattern of their own. I don’t understand why they do, but it didn’t change in the wet finishing process.

The first one in this batch, the overshot towel, will be the one that goes to my blogiversary giveaway winner. There are a few more hours to get your comments in before I pull the winning name tomorrow. Come back here & I’ll update the post with the winner’s name.
*******************************************
On Monday, known to some as Dyngus Day and to others as April Fool’s Day, I cut up paper into little pieces. I wrote each commenter’s name a piece, folded it in half, and dropped it into a brown paper bag. I shook the bag right side up, upside down, and sideways for about two minutes. Then I asked Red to draw out a single piece of paper, but that little dog would have none of it, so I did it myself. And the winner is……..drumroll………..Nancy!
I’m emailing you, Nancy, with the good news. Email me back with your mailing addy & I’ll send you the towel. CONGRATS!