I got Summer’s baby blankets wet finished and binding sewn on. Then I got it with a stomach bug (thanks, R) that had me down – luckily only for 2 days – so the completed blankets sat waiting for me to get them in the mail.
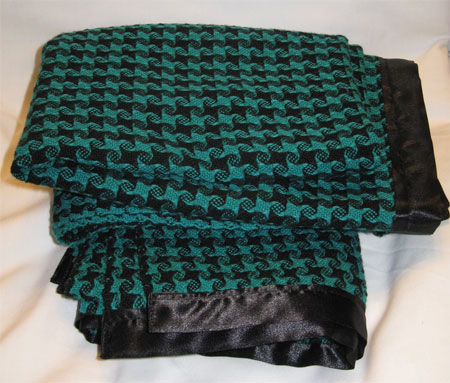
As soon as I was able to do that, I started on my next project…another sample baby wrap. Two of my 3 testing mamas concurred that sample wrap #1 was too thick. That’s good news for me–reducing the thickness means fewer threads per inch, which means less time measuring, beaming, threading, and beating. Since I’d dramatically underestimated how many ends and picks per inch I’d need when I began giving price estimates, I was hoping this would be what I’d hear.
I gave a LOT of thought to what colors and weaving pattern I’d choose for sample #2, since it wouldn’t be simply an addition to someone else’s choices.
Finally the obvious answer struck me. I’m warping in solid cream. This way I can time how long it takes to measure a solid color warp and use that as a basis for my time & pricing when moms order multi-colored warps. I’m going to use the same threading as for the hearts pattern, but with a different tie up and treadling so I don’t get bored.
I’m setting this sample at 26EPI (34 for the selvedges) as opposed to the 30 & 40 I used for sample #1. If it’s still too thick, I’ll go down further, but I don’t want to drop too much too fast.
I thought I’d also wind this sample warp long enough for 3 wraps, planning to weave each one with a different solid color weft. Since my goal is to be able to warp for 3 wraps, best I do it with my sample than when I’m working on someone’s order.
In the meantime, I rented a larger & more stable warping mill from the Rochester Weaver’s Guild. It’s pretty much identical to the modifications I think I want made to my own mill, so I figured I’d see if I was right.
So I did all my math, and measured out my guide string at a whopping 737″ – about 20.5 yards. I wound my first bout (group of threads) that long, and could only get 100 threads on the mill before it was too full to proceed. It was definitely not easy to get that many threads that length, and it took far too long – an hour. At that rate, it would take me 8 hours just to measure the warp! And this without knowing if my improved beaming process would go smoothly for that length or if I’d end up cutting off a bunch of warp anyway.
So I made a decision…with my tools and equipment, I simply cannot warp for 3 baby wraps at once. Two is my limit.
I made the adjustment in length to my guide string – it’s still 511″ – a bit over 14 yards long. I wound a second bout of 174 ends in about 45 minutes, and with much more ease than the longer one. Then I figured I’d better do some more math and determine if my time really was more efficient with measuring the shorter warp. Yep. I got about 48 yards/minute (a rather bizarre thing to measure, I know) at the 511″ length and only about 35 yards/minute at the longer length. That confirmed my decision.
So I wound a third bout – again at the 511″, and had the same positive experience as bout #2. Now there’s no doubt that I’ve made the right decision. I’ve got about half of the threads for tester wrap #2 measured, and can’t wait to get it all ready for my improved beaming process — which worked like a charm on Summer’s baby blankets, but the warp was so short that it wasn’t a good test.
Stay tuned to baby wrap central as my warping, learning, and testing continues!