MP, the woman who gave me my first order for a custom baby wrap and one of my testing moms, asked me to do a semi-random gradient for her next warp. I owe her a lot, so said yes, even though I was quite hesitant about how much time it would take to measure the warp.
Although I could be wrong, I think that the people who do gradient warps have sectional warp beams, which entails entirely different warping equipment and methods than mine.
Anyway, for MP, I said I’d give it a shot. I used a 60-thread pattern on the mill to get from all one color to all of the next. (All A, 1B, 4A, 1B, 5A, 1B, 1A, 1B, 1A, 1B, 6A, 2B, and on.) I wasn’t obsessive about sticking with the exact pattern when I was threading – since I wind 2 threads at once, I allowed myself to pick whichever one I wanted off the lease sticks at the loom.
Here’s the first bout of her warp on my mill. I really like these two colors – turquoise & aquamarine.
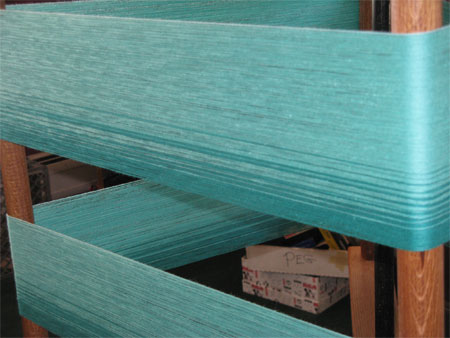
I forgot to take photos of bout numbers 2 & 4, but here’s #3 – charcoal to mauve.
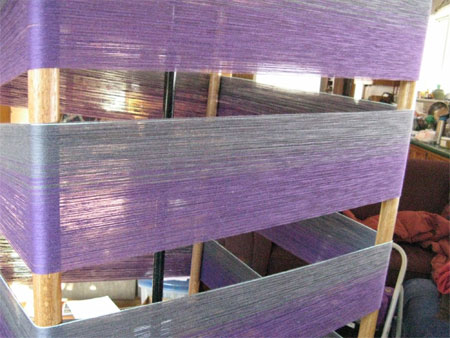
I got the loom all threaded up, and now have the first wrap about half woven. Black weft, hearts & flowers weave pattern.
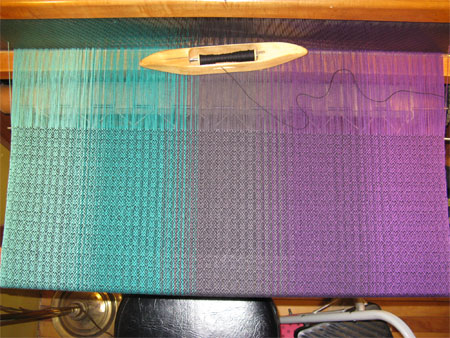
While I like the way this weave looks, it’s not my favorite to weave since it requires 2 floating selvedges. There is obviously some small movement I make that causes me to break the right hand floating selvedge thread about every 20″. PITA!! I’ve tried to study & correct it, but so far, no such luck.
Here you can see how the gradient works and a closeup of the pattern.
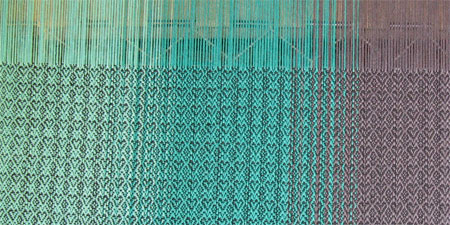
I think you can appreciate the gradient better on a plain weave than a pattern weave, but that’s just my opinion. Since I’m doing custom weaves on all the baby wraps, I weave what mama wants.