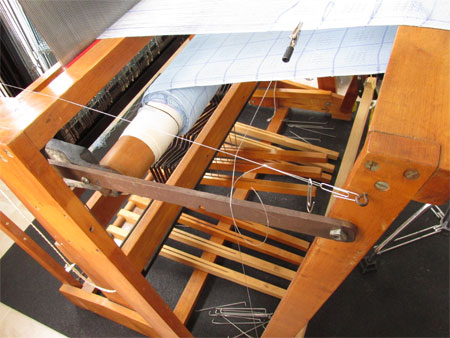
I admit it. I don’t usually use a temple. (It’s a tool designed to pull the selvedges [sides] of the weaving out toward the sides of the loom.) I know plenty of weavers use them every single time. Me? I use one rarely. Mostly when I’m getting too much draw in (when the weft threads pull too much on the end warp threads, making the actual width of the weaving less than the width in the reed/beater bar) and breaking threads near the edges.
I don’t own a ‘real’ temple, one manufactured specifically for this purpose, generally made of wood, and adjustable for different weaving widths. So when I need one I use a quick homemade version using alligator clips, fishing line, and washers. I’ve used those alligator clips on 30/2 silk with no ill effects. Usually I simply lay that fishing line over the side bar of my loom, but for the curtains, since they are almost as wide as my loom, that made the temple pull the fabric down too much as opposed to just out.
So I tied fishing line onto the back beam, then hooked it to eye hooks already in my front beam using paper clips. (I didn’t want to tie it to the front beam since it folds down to the floor when I’m threading and I’d have to cut the fishing line each time.) Initially I used a large paper clip, but as the fishing line stretched I switched to a smaller clip to take up more slack.
Where do the washers come in? I hang them from a paper clip tied to the alligator clip. Usually 3 washers does the trick. But not this time. I needed far more weight. But how much?
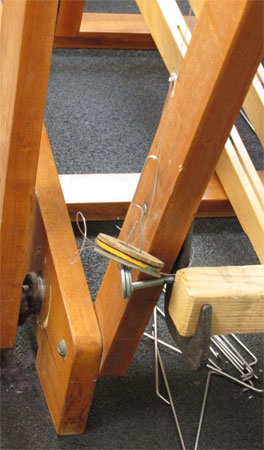
I found the LeClerc Clip Temple, and saw that their weights range from .4 pounds to 1.5 pounds. My 3 washers only weighed about 2 ounces total so I needed to add quite a bit. I’d recently found some really big, heavy washers on my walks (wonder who lost them from what…they weren’t all in the same place or on the same day) so added 3 of them to each side. That seemed to be a good amount.
My temples cost me….ummmm…virtually nothing. I had all the supplies hanging around the house. LeClerc’s Clip Temple? A whopping $83 plus shipping! Now obviously they’re not giving you rusty bits of metal and bent paper clips, but hey. $00 vs. $83? I’ll pick free and a bit of rust any day.
Back in December when I got my new aprons I used the ties that Macomber sent me with them. I wasn’t sure if I liked them, and after living with them for a few warps decided I didn’t. I went to the craft store around the corner from me and bought some waxed cotton string and went with the type of continuous apron strings I’d used before.
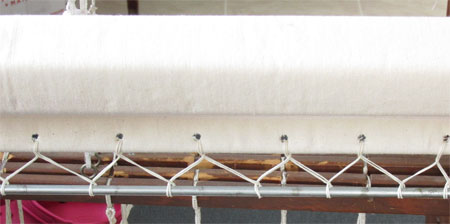
I do like this configuration better, but I didn’t like working with the waxed string. It’s too ‘sticky’ and doesn’t adjust across the width as I’d like it to. One of these days I’ll remember to buy some strong cotton string at either the hardware or craft store and re-do them.
Back when I lived in the sticks I had hardwood floors. I loved them. I felt badly that both of my looms – the little counterbalance and the Macomber – damaged the finish on those floors. I most decidedly did NOT want that to happen in my lovely new house, so I had to come up with something to put under the looms to protect the floors. Rugs in a weaving studio tend to be a bit of a pain and/or problem because weaving makes a mess…threads and fiber dust.
It was easy enough to figure out that a home gym mat would be good under the counterbalance. The loom is small and lightweight and would fit well on a standard sized mat – $42.
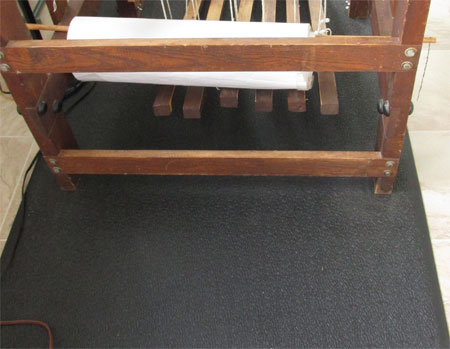
But I the Macomber presented a real challenge. First of all was the weight—that loom is heavy and I believed it would compress the type of mat I got for the counterbalance immediately so that there would not be any real floor protection. Then there was the size. The Mac would need two mats. Two very thick mats. The dollar signs were adding quickly. I don’t remember exactly what I was looking at, but I think it was in the neighborhood of $225. Then one day I was reading Amazon reviews for thick mats and someone wrote a really helpful comment – instead of spending major dollars for this mat, the writer bought a horse mat. WHAT?!
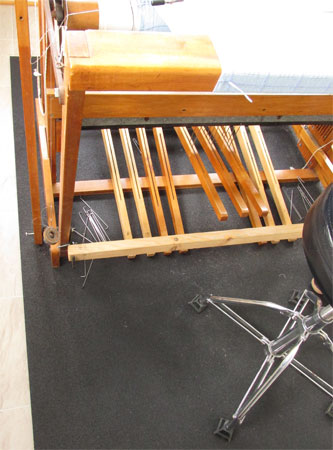
I checked with my local Tractor Supply store. They carried mat designed for horse and cow stalls in a few different weights and widths, and cut them to the length you needed. I spent $52, including tax! This was a scathingly brilliant idea! (Phrase stolen from Hayley Mills’ character in The Trouble with Angels.) Thanks, Amazon reviewer! I’m positive I never would have come up with that.
I’m still hoping more readers tell me about your unconventional tools. If not for weaving, then for your kitchen, home, or car.