|
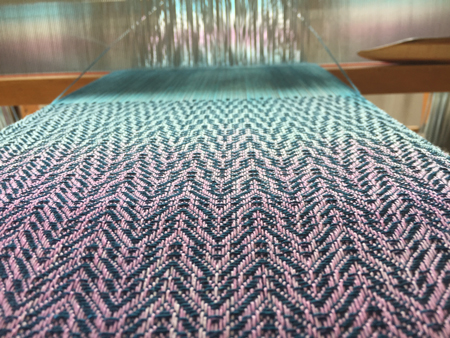
I’ve enjoyed taking close-up shots of my scarves on the loom lately. This one gives the impression of 3-dimensional hills and valleys. At least it does when it’s large, maybe not so much at a small size.
It’s the first scarf I wove on that hand painted tencel warp, and I used the weft I’d immersion-dyed for the warp a few weeks ago but decided not to use. It matched the darker blue of this warp very well. I liked it on the loom ok, but not so much in the finished scarf. Too dark for my tastes.
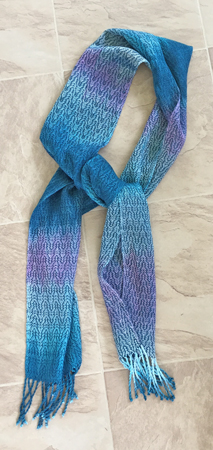
After that I had to cut and re-tie my warp. Not sure why I was having problems with it, but easier to do this than to fuss with it every pick for the rest of the length.
From my notes I knew I’d measured the warp to make 1 fringed scarf, 1 long cowl, and 1 short cowl. I knew I’d lose some length by the cutting and re-tying, so decided to do the short cowl next. Once I got this woven I’d simply use whatever length was left for the long cowl. So I picked a commercially-dyed tencel that was almost exactly the same color as the medium blue in my warp and treadled for Ms and Ws.
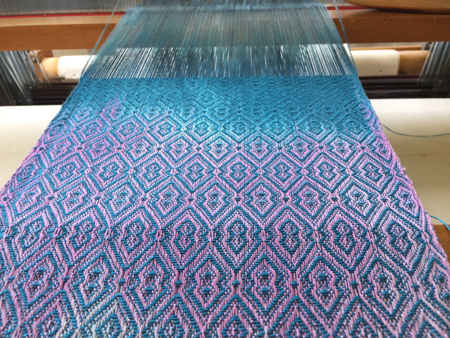
I really like the way the colors play together in this piece, and find myself liking these short cowls. Yes, there are fewer options for wear, but they are light and easy to toss on. Anyway, I do wish that the purple color had shown up again in the warp, but c’est la vie.
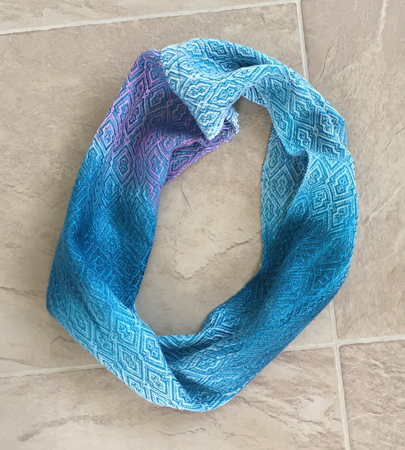
For the long cowl I picked a commercially-dyed red-violet that looked great when I held it next to each color in the warp. Interestingly, it turned almost burgundy as I wove it, using what I think of as my feathers treadling.
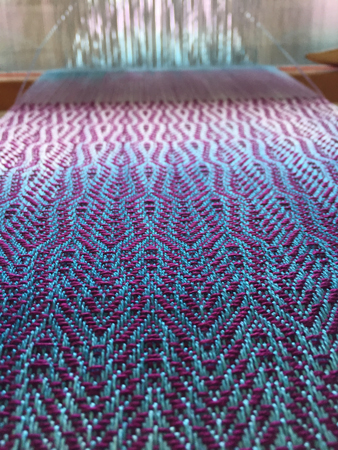
I’m happy with it, although I still like the colors best in the short cowl. We’ll see what my customers think at my next show…just a month away now.
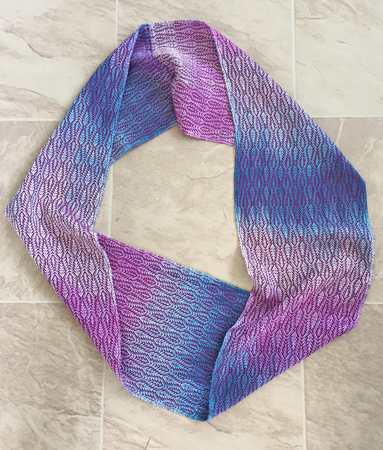
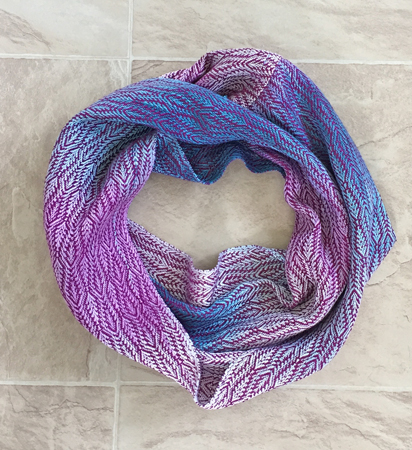
This morning my son and I went to a U-Pick place. We got several pounds of sweet cherries and LOTS of blueberries.
I came home and made jam.
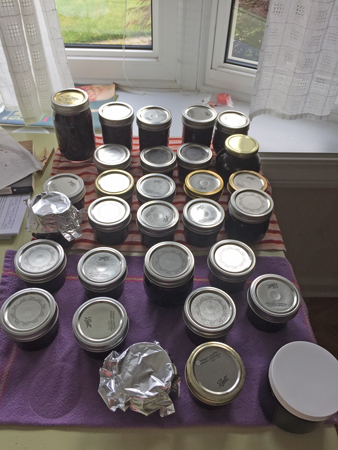
First up, closest to the window, is cherry-orange-spice jam, cooked with 2 cinnamon sticks, some whole allspice and whole cloves in a tea ball. I’m guessing that it won’t set well, but will hopefully taste good. I got 1 pint, 5 half-pints, and 4 half-cup jars. (1 already sent home with son.)
Then I made a batch of blueberry-ginger. I followed a recipe for the amount of freshly-grated ginger (1.5 teaspoons), and I’m pretty sure you can’t taste it at all. I got 3 half-pints and 8 half-cup jars of that.
Next another batch of blueberry, this time with double the ginger (1 tablespoon) plus 3 tablespoons of fresh lemon thyme. That got me 2 pints (1 already sent home with son) and 9 half-cup jars.
Plus, I sent home probably 6 cups of blueberries with my son, and I have another 2 cups here to just eat.
I’m confident that the blueberry will all set, but even in that second batch, all I taste is blueberries, but maybe more discerning palettes can taste more.
Still, they’ll be good, and some will make nice gifts.
Left the house at 10AM to go pick, and by 4:30PM all the jam was made and the kitchen was cleaned up, except for cooling, labeling, and putting away the fruits of my labor (yuck, yuck).
Earlier this month I blogged about some 10/2 tencel I had dyed and put on my rigid heddle loom for demonstration at a show.
After I took that photo of the 2 heddles threaded, I tied on to the front of the loom and did a few weaving experiments. I quickly learned that at a show was not the time to use the 2 heddles independently as too much thought was required. So I clamped them together to weave as 1, with double density of 22 ends per inch and off I set.
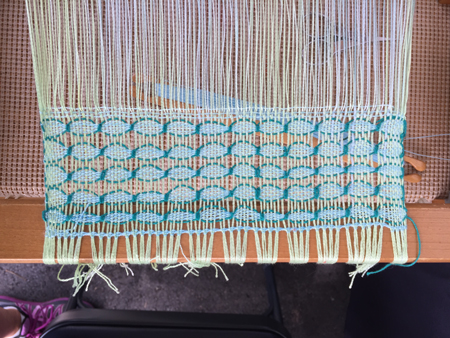
I started with 5 rows of Danish medallions. I’d never woven them before, but as usual, that didn’t stop me. The first motif got quite squished as I wound it on the front beam. Hmmmmmm, I wondered.
Then I simply wove plain weave. Because of the double density, it was actually more like basket weave, with 2 warp threads side by side in each shed. I didn’t get much woven in the 3 days of the show because I was encouraging people to weave on the tapestry loom (more of that in an upcoming post), only about 10″.
I hated it. It was clear to me that it would produce a sleazy fabric, one that would not stand up to regular use and that I would not be willing to sell.
So when I came home I put a set of lease sticks in the warp, unwound and unwove what I’d done, getting back to the beginning of the warp.
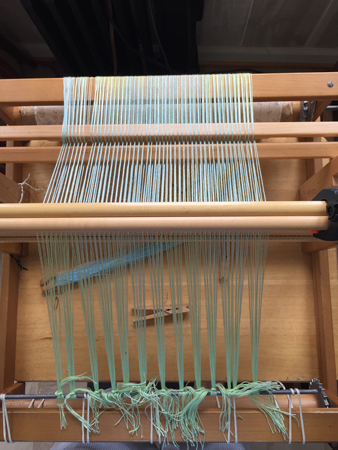
Then I untied, carried it over to the Macomber, and beamed it.
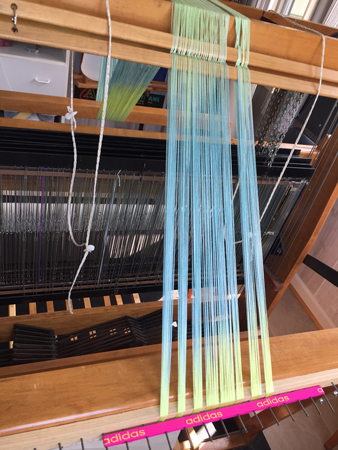
For the first scarf I used the pale blue I’d immersion dyed to match/coordinate. Although I only sett it at 24 ends per inch, the fabric was turning out fine. I can’t really explain this, I just accept it.
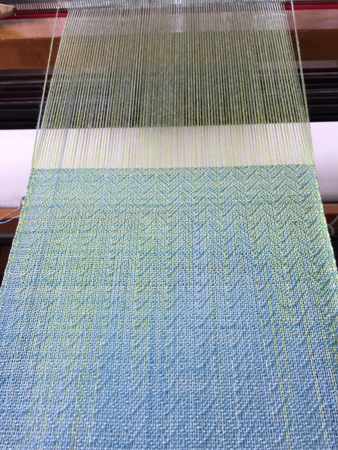
For the second scarf, which would be a cowl, I used a commercially dyed tencel. I really like the texture – actually the appearance of texture – in this shot.
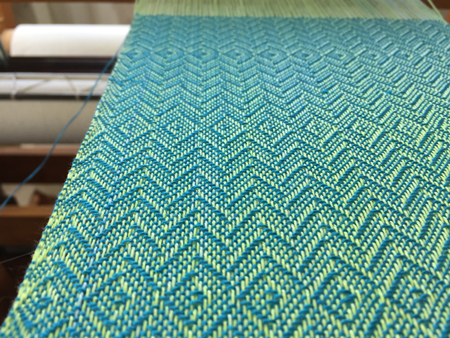
This morning I fringed the scarf and sewed the cowl, subsequently washing, drying, and pressing them.
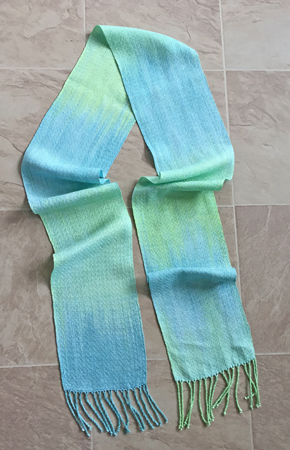
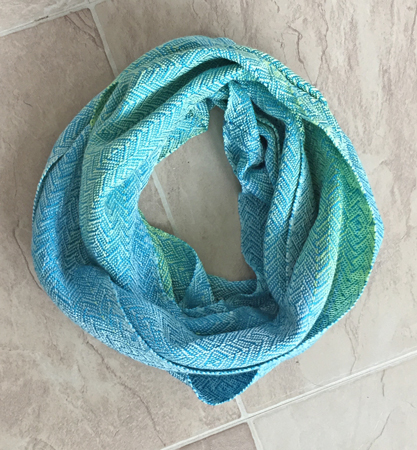
Although these colors are much lighter than my usual palette, I think they’re perfect for summer. So much so that I decided to use similar colors for my next project.
I measured out 4 bouts of 30/2 silk, 216 ends each, long enough for 2 shawls. I knew that this silk would need a really good scour, and it sure did; look how dirty the water was!
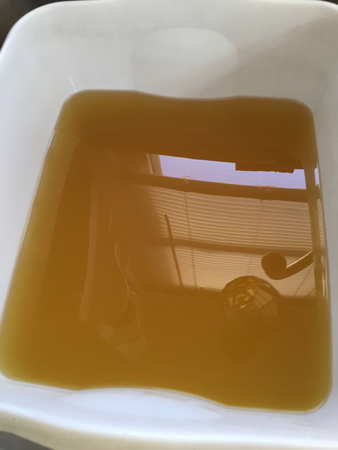
I mixed up some dyes, using some leftover blues from the scarf warp, went down to the basement at 5PM yesterday, and came back upstairs around 8 with my painting and clean up work complete. Look how much blue and green dye I had when I was done with the painting – NONE! Good thing I didn’t need more – although I could have come close with the greens as I’d measured that, I never could have matched the blues since I was using up leftovers.
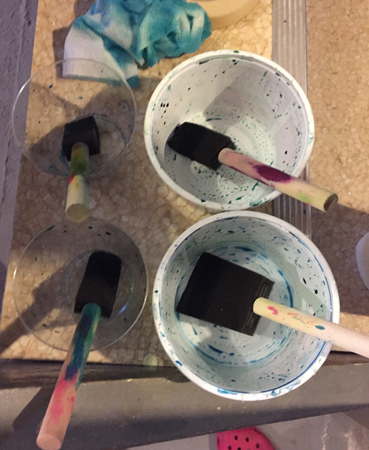
After steaming, overnight batching, and rinsing, here is the dyed silk hanging on the line along with the tencel scarves. You’d think I’d planned that similarity or something! 😉 In reality, I’m not good enough to claim that – a happy accident.
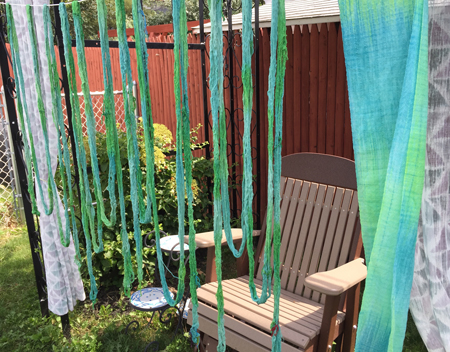
Here’s what’s going on the loom today, from dyeing I did back in April. These are more my typical color values.
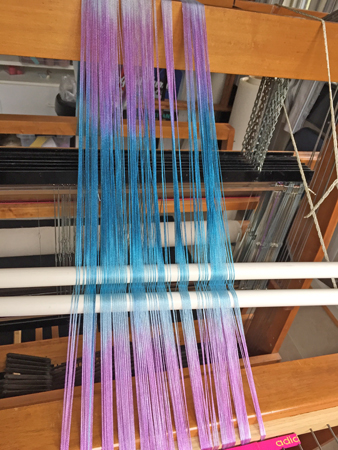
I got everything done that was on my list. All that’s left for today is to go pick up and load the rental van and drive.
I managed to fit in weaving 3/4 of the first of those custom baby wraps, with a white weft.
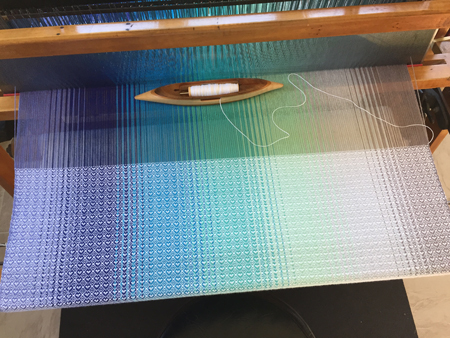
The warp will make 3 wraps, each pretty short at only 2.3 meters, meaning I only have to weave 110″ apiece. The first wrap has that white weft, the other 2 will have charcoal wefts.
I looked at the dates involved and breathed a sigh of relief. I had promised the moms that I’d have the wraps woven within 3 weeks of receiving the yarn. The box of yarn arrived on June 27, so I’ve got until July 18 to do the weaving, hemming, and wet finishing. No sweat.
So back to this weekend…the weather forecast in Chautauqua is for rain – most of the day Friday and all day Saturday. It looks like it might clear on Sunday, so I’m crossing my fingers that I’ll be packing up dry. However if it does, in fact, rain for 2 days, I likely won’t be able to do everything I’d planned. Although I have awnings for my tent, depending on the wind strength and direction, I may have to have the sides of the tent down, which dramatically limits the space available.
But I couldn’t know that as I was preparing, so I have the rigid heddle loom and a tapestry loom ready to go. Actually, the tapestry loom has a story behind it. I intended to use the little picture frame loom I bought from my weaving teacher. But when I pulled it down, I realized it was too small for 3 days of weaving at this show, where people can hang around for some time, as opposed to street shows where people move rather quickly.
So I lucked out when I saw this frame for a laundry bag by the curb several blocks away.
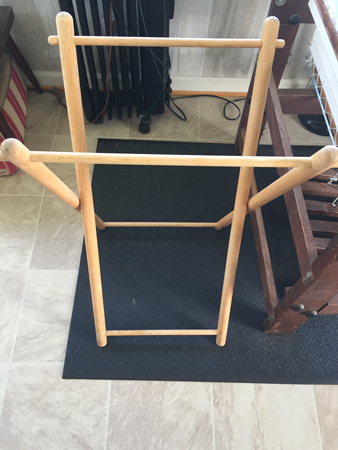
I snatched it up, took it apart into 2 big rectangles, consulted with the weaving teacher about the ends per inch I should use, and warped it up with carpet warp.
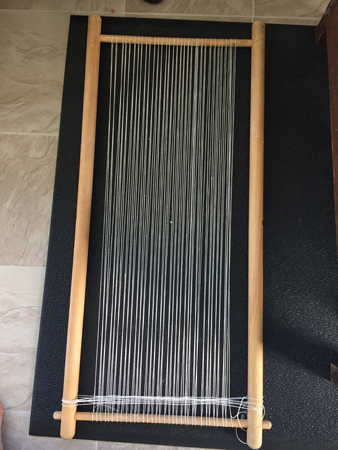
I do hope we get to use it this weekend. This is SOOOOO much easier than the frame looms I crafted for previous community weaving! And now I have TWO of these laundry-bag-holder-looms. I will use them in the future, I’m sure.
Like anyone in business, I have to prioritize. What has the closest deadline? Do those things first. So here’s what I’ve accomplished since my last post…4 days ago. (You know that saying, if you want something done, give it to a busy person? Yep.)
- Wash & dry a bunch of pillowcases and other fabric, then cut them into appropriate sizes, sew 31 bags, print and cut my bag tags, then thread the bags with ribbon and tie a bag tag on them. (no pix)
- Do both the machine and hand sewing on those 8 bumberet towels, then wash and dry them. They still need the hard press, but that won’t take long. (no pix)
- Thanks to my son, get the 2nd heddle kit installed on my rigid heddle loom.
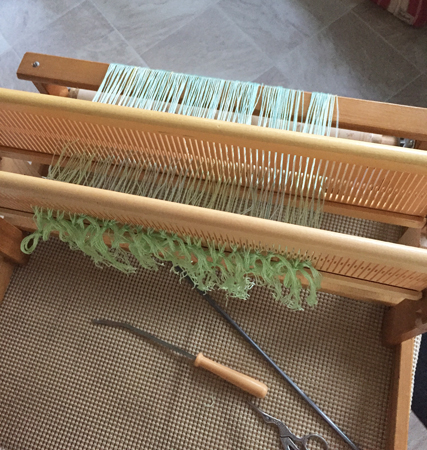
- Get the heddles and reed threaded, and the treadles tied up, for that custom baby wrap order.
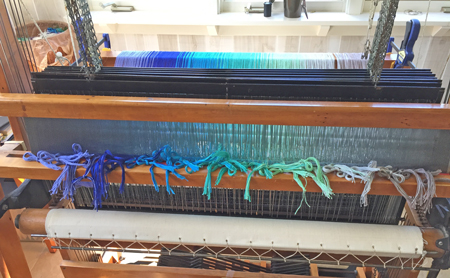
- Get a warp prepped, dyed, and threaded on that RH loom. This is a story in and of itself.
Here’s another saying, this time a bit modified: If at first you don’t succeed, dye, dye again.
After measuring out a 10/2 tencel warp, I went down to my basement and hand painted it in cool blue and 2 greens, thinking they were perfect colors for summer at the lake, where my show will be next weekend.
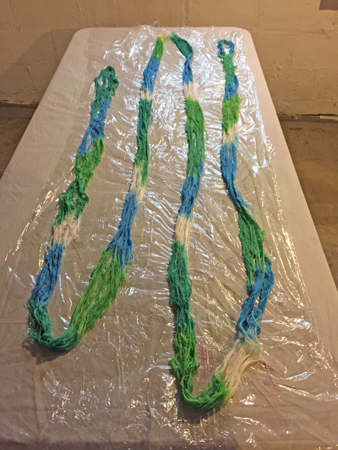
I was happy with it. Until after it batched and was rinsed. The greens were ok, but the blue was WAY too pale. So after consulting with a great dyer I know, I laid the wet warp back out on the table, mixed some more concentrated dye with the soda ash so I could skip the pre-soak step, and painted over the blue. I also decided to eliminate the unpainted/white areas, since the colors were pale. Here it is in process.
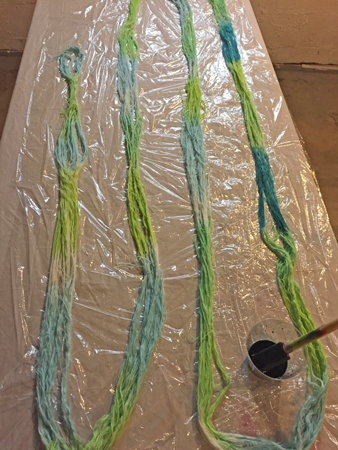
Meanwhile, I wanted to dye the wefts to coordinate. So I measured out 2 small skeins, just under 2 ounces each, 1 for the weft for each scarf. I immersion dyed these wefts before I knew how the warp would turn out. Since the skeins were so small, the dishpans I usually use as vessels were too big to be practical. I searched around the house for smaller containers that I wouldn’t need again, and ended up at my neighbors, too. The end result? I was dyeing al Fresca. (Get it?)
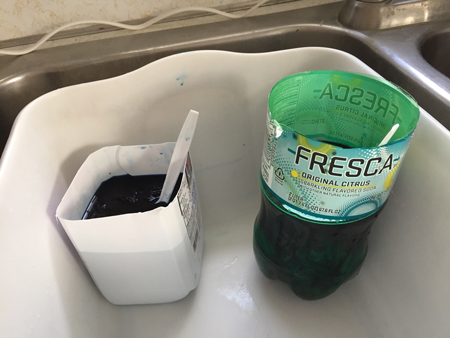
After all the yarn was dry, I didn’t think the wefts were right for the warp, so I wound and dyed a third skein. Here’s how things proceeded…
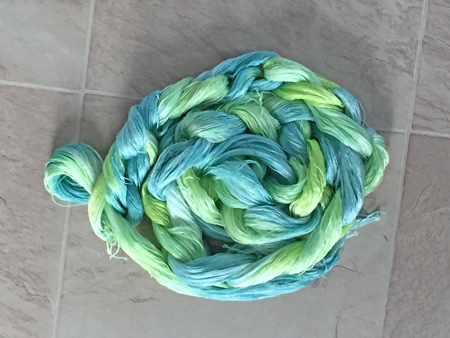 First, the hand painted warp
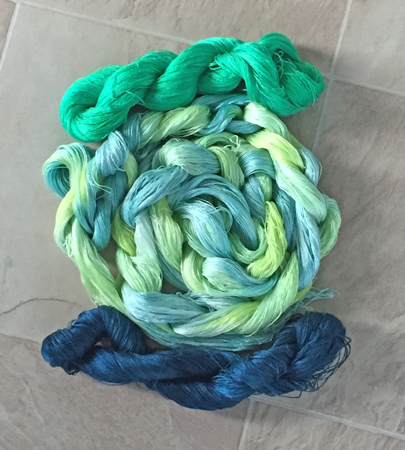 Next that warp with the first 2 wefts I dyed
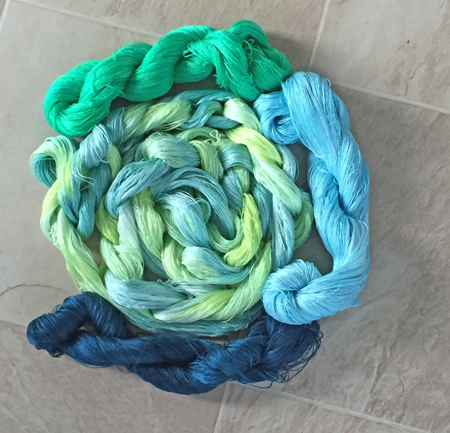 Then with the 3rd weft I dyed – this one is perfect, righ?
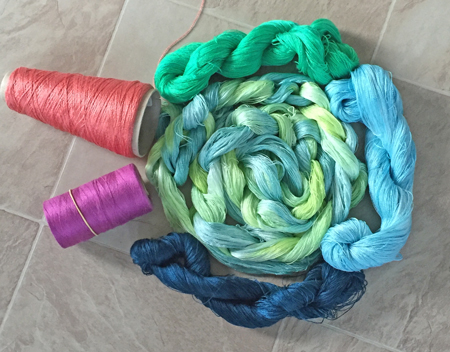 I looked through my stash and added 2 more potential weft colors. All will need to be auditioned on the loom.
I’m still not sure if I have the 2nd weft color yet, but won’t dye any more. I’ll have to use one of those colors or find something else in my stash.
Here’s what’s left to do by Wednesday evening:
- Make a cake for my son’s birthday on Monday, and enjoy a family dinner tomorrow night;
- Make something nice to bring to a dinner with friends on Tuesday to celebrate the 4th;
- Tie on that RH warp so I can test out wefts and decide what to bring to the show;
- Warp up my little tapestry loom, also to bring to the show, with a variety of yarns for people to do a bit of community weaving while I’m there – anything to bring people into my booth;
- Hard press and label those towels;
- Begin weaving that baby wrap – I made a time commitment to those women.
Think I can do it? I’m sure I can. It’s all about time management.
|
|