…to show, just on the weaving front. Weaving like mad to get ready for my last summer show later this month, plus doing the regular things like seemingly non-stop lawn mowing. But enough of that. Here’s what you want to see. I hope. In chronological order.
A fellow Guild member is moving so had a sale at her house of some yarns, books, and equipment. I behaved myself, but did spend some money. And what I bought inspired me. I bought a cone of orange cotton yarn plied with electric blue metallic. Had to use that in some scarves!
I thought I wanted to do bumberet scarves, but after some planning and playing decided I’d do some random stripes and a simple straight twill instead, thinking it was a better use of the bling yarn. I used the random stripe generator at biscuitsandjam. Once I had a stripe arrangement I liked, I set it up on my counterbalance loom. First I used a burgundy weft.
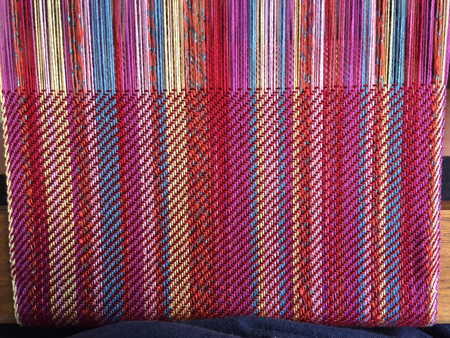
The second scarf had a medium blue weft. This is my personal favorite of the trio.
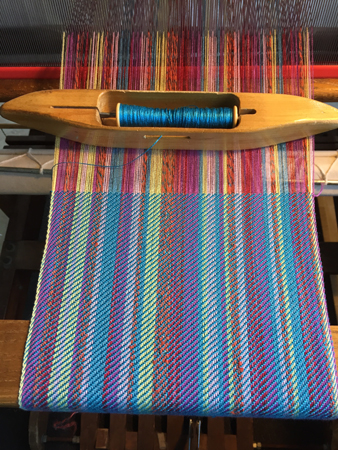
Finally I went with the knowledge that black intensifies color, so chose a black weft. I don’t really care for what it did; maybe someone else will. These 3 scarves are fringed and wet finished.
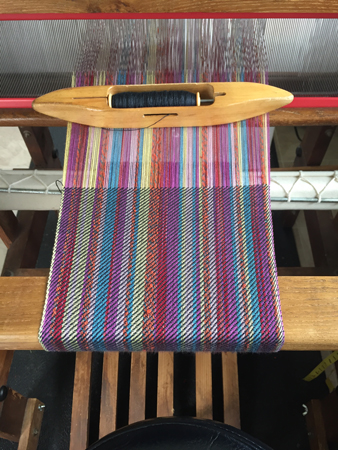
Another cone of yarn I bought was this really highly textured, undyed cotton. It spoke to me. I pulled out my 8/2 undyed cotton, alternating it with some yarn I’ve had for a long time, and bought who knows where from another weaver. The cone is ancient, and when I bought it I did the burn test and labelled it rayon. I did the burn test again last week and determined that it is not rayon, at least not today’s rayon. I’m going to mark the tag vintage synthetic.
Anyway, the vintage yarn is quite fine – about 5,000 yards per pound, and VERY shiny. So I thought it would make an interesting weave with unmercerized cotton. I wound them together and threaded them together – 1 strand cotton and 1 strand synthetic in each heddle. Here’s what it looked like while I was beaming it. Can you see the sheen of that yarn? Cool, huh?
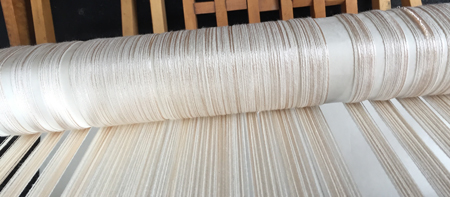
I wound a warp for 2 shawls, and only had enough of that nubbly yarn to weave 1. I decided to use both the nubbly yarn and the synthetic in each pick. Here’s how that looked on the loom. I’m soooo happy with it. You can’t really see the undulating twill pattern, but that’s okay with me.
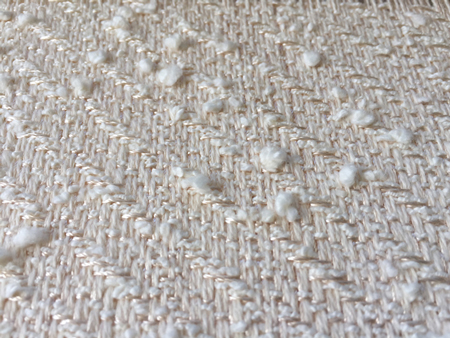
For the 2nd shawl I tried out a few different wefts. My favorite was to simply use the same yarns for weft as for warp. I am just in love with this, too.
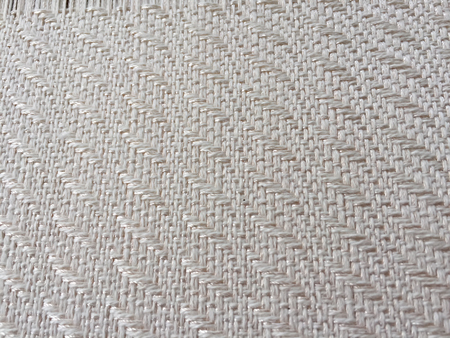
In addition to looking great, these shawls have a wonderful hand. They are soft and drape beautiful, with enough weight to be luxurious. These shawls are also fringed and wet finished.
Next up I moved away from the new yarns, putting on a silk warp for a set of 3 complex twill scarves. First in black and white.
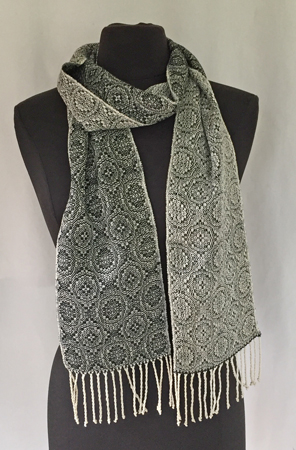
Next in royal purple.
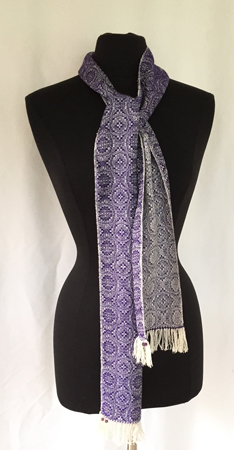
I knew that I’d planned for this to be a long cowl, and subsequently decided I didn’t want that, so I had to make the fringe short or I’d run out of warp. So without enough length to make twisted fringe, I decided to add some beads, using both glass pearlized seed beads and small amethyst rounds.
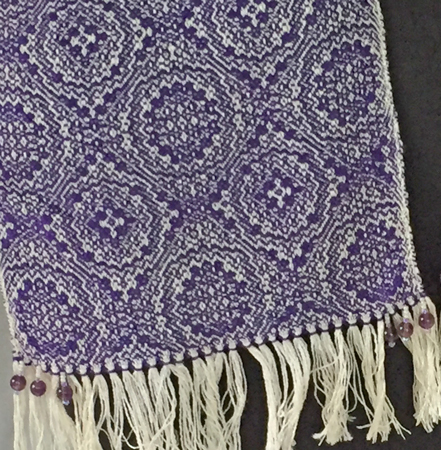
I only had enough length for a short cowl, and chose red weft and a different treadling pattern. Obviously these are also all finished.
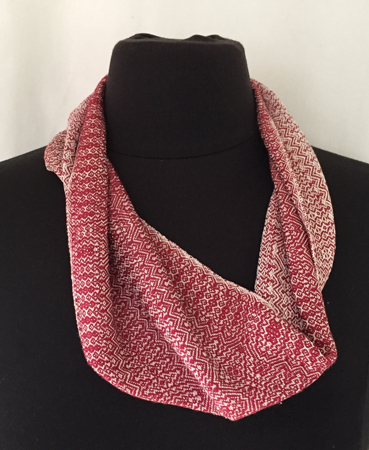
Then I wanted to make some more tencel scarves, so I measured out white tencel for more complex twill.
First, again, black & white. This time squares.
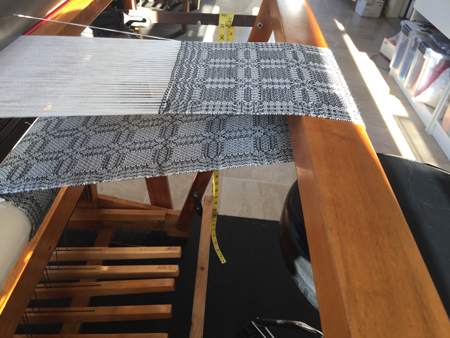
Next up a sage green, with the squares elongated to rectangles.
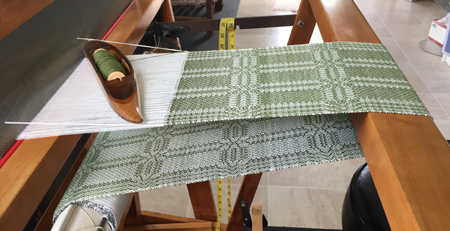
For the third I changed the tie up, and wove with coral & white, back to squares.
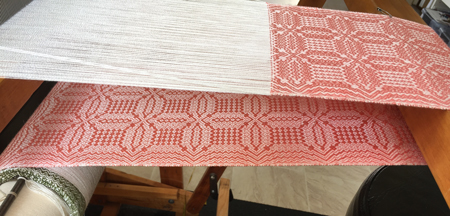
I was sorely disappointed that I ran out of that coral yarn about 6″ before I wanted to be done. This scarf will be a little shorter than my usual. These scarves are awaiting fringing and wet finishing.
Now I’m trying something new-to-me. A variegated cotton warp with a rayon chenille weft. I chose to only measure enough length for 1 piece, since I’m not sure if I’ll like it, even though that’s an inefficient way to weave. I’m going to sew this shawl into a moebius when it comes off the loom. We’ll see if my customers like that.
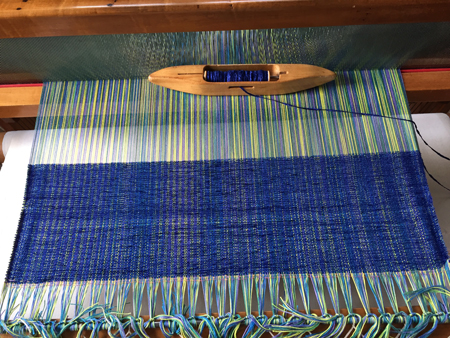
I don’t plan to weave other things before the show as I have other commitments. But I still have to label everything and make more bags. Plenty of time, she says. 🙂