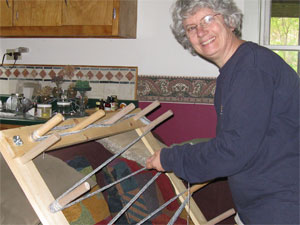
| Handweaving starts with preparing the warp - the yarns that make up the length of the scarf. This process makes all the yarn that I'll put on the loom the same length. Like most weavers, I use a warping board to do this. I'm lucky that my wonderful son made this one for me. I can easily make warps up to nine yards long with this board. Next time he comes home for a visit, I think I'll have him make a slight modification so I can make even longer warps. |
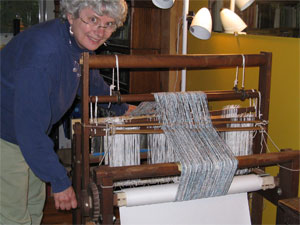 | Once the warp is prepared, it has be put on the loom. In this step, called beaming the warp, yarn is carefully wound around the back beam of the loom. It takes a lot of time to make sure that I don't have any twists, tangles, or pulls. Lining my yarn up exactly is critical to avoid lots of problems later on. |
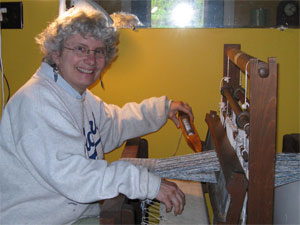 | Finally, the fun part - weaving! This is where a Zen-like rhythm sets in, with my hands and feet working in tandem. Throw the shuttle, beat the yarn, change the heddles, throw the shuttle beat the yarn, change the heddles, repeat 12-16 times per inch for the length the scarf. I work on a lovely, vintage loom, likely more than 60 years old. (Even older than me!) Handmade of black walnut, it's a small, counterbalance, floor loom, somewhat unusual in the 21st century, but the workhorse of its day. It was a real pleasure to give my gem of a loom the tender loving care, time, and attention it hadn't seen in decades. I had to replace its original handmade heddles, replace all the ties, sand and wax the moving parts, and more - all to give the loom its own second wind. My beautiful loom is quiet, comfortable, and operates smoothly. And I love the poem that one of its prior owners taped onto the top... |